【いまさら聞けない鉄道技術用語】進化し続ける鉄道車両の「ステンレス車体」
鉄道車両の車体としては一般的になったステンレス車体。いまではメーカーごとに独自に進化し、細かな違いも見られます。
そもそも「ステンレス」とは?
ステンレスは鉄(Fe)を50%以上の主成分とし、クロム(Cr)を10.5%以上含んだ合金です。鉄道車両では鉄、クロム、ニッケルを含有したオーステナイト系のSUS301やSUS304を使用。延性、剃性に富み、深絞り、曲げ加工など冷間加工性が良く、溶接性に優れています。
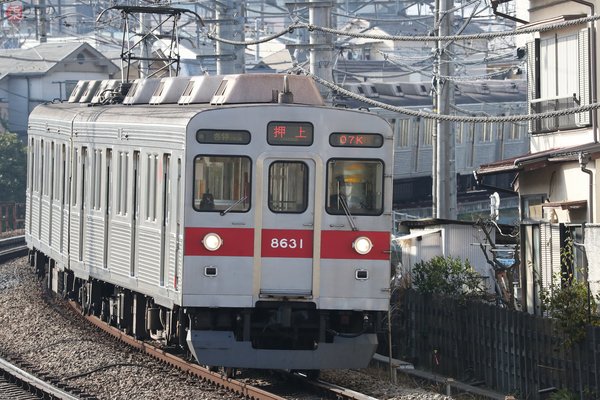
ステンレス最大の特徴は腐食に強いことで、ステンレスの表層に形成された不動態皮膜という保護酸化皮膜がステンレス腐食の進行を防いでくれます。不動態皮膜は鉄に添加したクロムが酸素と結合して形成します。その厚さは1~3nmと非常に薄いのですが、表層に傷が付いても酸素があれば自己再生します。
腐食に強いため長寿命化が可能。また、腐食による板の“痩せ”を考慮する必要がないことに加えて高強度のため、板の厚さを普通鋼より薄くすることができ、普通鋼製車体よりも軽量化できます。
光沢が強くて汚れが目立たないため、塗装が不要なのもステンレスの特徴です。塗装工程や塗装設備、塗料代を節約できるので製造コストや維持コストの抑制が可能。工場への検査入場期間も短くでき、運用効率もアップします。
なお、最近のステンレス車は無塗装車体の強い光沢を抑えるためにダルフィニッシュ仕上げやベルトグラインド仕上げを施すのが主流となっています。もちろん、塗装することも可能で、実際塗装されたステンレス車も多数存在します。カラーフィルムを車体全体にラッピングしたステンレス車両もあります。
ステンレスが普通鋼より不利な点は価格が高いこと。ステンレス1kg当たりの価格は普通鋼の約4~5倍にもなります。とはいえ、ステンレス車体は維持費が安くて長寿命ですから、長い目で見ればそれほど高くはないといえるかもしれません。
セミステンレス車体の基本構造
ステンレス車体は大きく分けて、セミステンレス車体とオールステンレス車体の2種類あります。どちらも車体構造は基本的に同じで、台枠と支柱や垂木などの骨組、そして外板で構成された骨皮構造となっています。
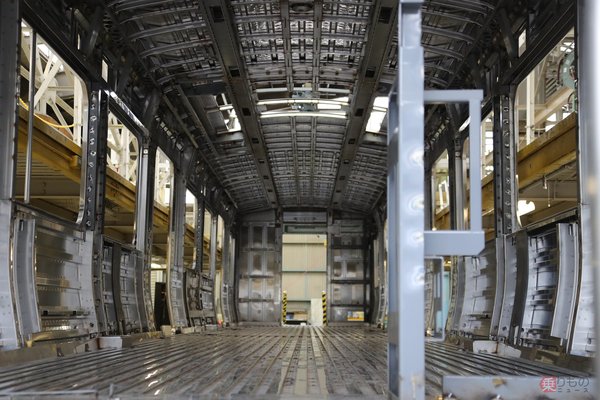
セミステンレス車体は普通鋼製の台枠や骨組にSUS304ステンレスの外板を貼った車体で、スキンステンレスとも言われています。「スキン」とは「皮」を意味する言葉です。普通鋼車体の製造技術がそのまま使えるため製造が容易で、オールステンレスよりも製造コストを抑えられるというメリットがあります。
しかし、普通鋼とステンレスという異金属を溶接しているため、電食による構体部分の劣化が普通鋼製車体よりも早いと言われています。もっとも、実際にはかなり長寿命のセミステンレス車も存在しています。
オールステンレス車体は台枠や骨組にもステンレスを使った車体です。ただし台枠のうち連結器を取り付ける車端中梁、台車を取り付ける枕梁、重い床下機器を取り付ける横梁などには普通鋼を用いて剛性を確保しています。
セミステンレス車体と比べてさらに軽量化、長寿命化が可能となるオールステンレス車体ですが、専門的な製造ノウハウが必要で、1950年代に製造に関する特許を持っていたのが米国のバッド社でした。
そこで東急車輌製造(現在の総合車両製作所=J-TREC)はバッド社と提携。1962(昭和37)年に日本初のオールステンレス車として東急7000系を量産しました。以後東急7200系、8000系、8500系、京王3000系、南海6000系、そして静岡鉄道1000系がオールステンレス車体を採用しています。
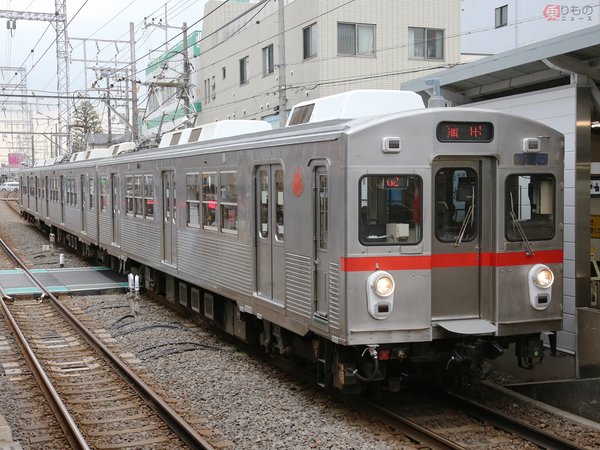
残り2408文字
この続きは有料会員登録をすると読むことができます。
Writer: 松沼 猛(鉄道ジャーナリスト)
1968年生まれのいわゆるブルートレイン、L特急ブーム世代。車両の形態分類と撮影、そして廃線跡が好きで全国各地を駆け巡っている。技術系から子ども向けまでさまざまな鉄道誌の編集長を経験。また、鉄道専門誌やウェブにも多数寄稿している。
コメント